石英ガラスの曲げ、または一般的には曲げ石英ガラスチューブは、特定のプロセスを使用して曲線状に成形された石英ガラスチューブを指します。
OD | ID | WT | L(mm) |
---|---|---|---|
1mm | 0.5mm | 0.25mm | 1~6000mm (カスタム) |
1.5mm | 0.8mm | 0.35mm | 1~6000mm (カスタム) |
2mm | 1mm | 0.5mm | 1~6000mm (カスタム) |
2.5mm | 1.5mm | 0.5mm | 1~6000mm (カスタム) |
3mm | 2mm | 0.5mm | 1~6000mm (カスタム) |
3mm | 1mm | 1mm | 1~6000mm (カスタム) |
4mm | 3mm | 0.5mm | 1~6000mm (カスタム) |
4mm | 2mm | 1mm | 1~6000mm (カスタム) |
4mm | 1mm | 1.5mm | 1~6000mm (カスタム) |
5mm | 4mm | 0.5mm | 1~6000mm (カスタム) |
5mm | 3mm | 1mm | 1~6000mm (カスタム) |
5mm | 2mm | 1.5mm | 1~6000mm (カスタム) |
5.5mm | 3.5mm | 1mm | 1~6000mm (カスタム) |
6mm | 5mm | 0.5mm | 1~6000mm (カスタム) |
6mm | 4mm | 1mm | 1~6000mm (カスタム) |
6mm | 3mm | 1.5mm | 1~6000mm (カスタム) |
6mm | 2mm | 2mm | 1~6000mm (カスタム) |
6.5mm | 4.5mm | 1mm | 1~6000mm (カスタム) |
7mm | 5mm | 1mm | 1~6000mm (カスタム) |
7mm | 4mm | 1.5mm | 1~6000mm (カスタム) |
7.5mm | 5.5mm | 1mm | 1~6000mm (カスタム) |
8mm | 6mm | 1mm | 1~6000mm (カスタム) |
8mm | 5mm | 1.5mm | 1~6000mm (カスタム) |
8.5mm | 6.5mm | 1mm | 1~6000mm (カスタム) |
9mm | 7mm | 1mm | 1~6000mm (カスタム) |
9mm | 6mm | 1.5mm | 1~6000mm (カスタム) |
9mm | 5mm | 2mm | 1~6000mm (カスタム) |
10mm | 8mm | 1mm | 1~6000mm (カスタム) |
10mm | 7mm | 1.5mm | 1~6000mm (カスタム) |
10mm | 6mm | 2mm | 1~6000mm (カスタム) |
10mm | 4mm | 3mm | 1~6000mm (カスタム) |
10mm | 2mm | 4mm | 1~6000mm (カスタム) |
11mm | 9mm | 1mm | 1~6000mm (カスタム) |
11mm | 8mm | 1.5mm | 1~6000mm (カスタム) |
11mm | 7mm | 2mm | 1~6000mm (カスタム) |
11mm | 5mm | 3mm | 1~6000mm (カスタム) |
12mm | 10mm | 1mm | 1~6000mm (カスタム) |
12mm | 8mm | 2mm | 1~6000mm (カスタム) |
12mm | 4mm | 4mm | 1~6000mm (カスタム) |
13mm | 11mm | 1mm | 1~6000mm (カスタム) |
13mm | 10mm | 1.5mm | 1~6000mm (カスタム) |
13mm | 9mm | 2mm | 1~6000mm (カスタム) |
14mm | 12mm | 1mm | 1~6000mm (カスタム) |
14mm | 10mm | 2mm | 1~6000mm (カスタム) |
15mm | 13mm | 1mm | 1~6000mm (カスタム) |
15mm | 11mm | 2mm | 1~6000mm (カスタム) |
15mm | 9mm | 3mm | 1~6000mm (カスタム) |
16mm | 14mm | 1mm | 1~6000mm (カスタム) |
16mm | 13mm | 1.5mm | 1~6000mm (カスタム) |
16mm | 12mm | 2mm | 1~6000mm (カスタム) |
16mm | 10mm | 3mm | 1~6000mm (カスタム) |
17mm | 15mm | 1mm | 1~6000mm (カスタム) |
17mm | 14mm | 1.5mm | 1~6000mm (カスタム) |
18mm | 16mm | 1mm | 1~6000mm (カスタム) |
18mm | 15mm | 1.5mm | 1~6000mm (カスタム) |
18mm | 14mm | 2mm | 1~6000mm (カスタム) |
18mm | 12mm | 3mm | 1~6000mm (カスタム) |
18mm | 11mm | 3.5mm | 1~6000mm (カスタム) |
19mm | 17mm | 1mm | 1~6000mm (カスタム) |
19mm | 16mm | 1.5mm | 1~6000mm (カスタム) |
19mm | 13mm | 3mm | 1~6000mm (カスタム) |
20mm | 18mm | 1mm | 1~6000mm (カスタム) |
20mm | 17mm | 1.5mm | 1~6000mm (カスタム) |
20mm | 16mm | 2mm | 1~6000mm (カスタム) |
20mm | 14mm | 3mm | 1~6000mm (カスタム) |
25mm | 19mm | 3mm | 1~6000mm (カスタム) |
25mm | 21mm | 2mm | 1~6000mm (カスタム) |
25mm | 21mm | 2mm | 1~6000mm (カスタム) |
25mm | 21mm | 2mm | 1~6000mm (カスタム) |
25mm | 21mm | 2mm | 1~6000mm (カスタム) |
25mm | 20mm | 2.5mm | 1~6000mm (カスタム) |
25mm | 20mm | 2.5mm | 1~6000mm (カスタム) |
25mm | 20mm | 2.5mm | 1~6000mm (カスタム) |
26mm | 21mm | 2.5mm | 1~6000mm (カスタム) |
28mm | 24mm | 2mm | 1~6000mm (カスタム) |
30mm | 26mm | 2mm | 1~6000mm (カスタム) |
30mm | 24mm | 3mm | 1~6000mm (カスタム) |
35mm | 30mm | 2.5mm | 1~6000mm (カスタム) |
40mm | 34mm | 3mm | 1~6000mm (カスタム) |
40mm | 34mm | 3mm | 1~6000mm (カスタム) |
40mm | 34mm | 3mm | 1~6000mm (カスタム) |
40mm | 34mm | 3mm | 1~6000mm (カスタム) |
40mm | 32mm | 4mm | 1~6000mm (カスタム) |
40mm | 32mm | 4mm | 1~6000mm (カスタム) |
40mm | 32mm | 4mm | 1~6000mm (カスタム) |
40mm | 32mm | 4mm | 1~6000mm (カスタム) |
40mm | 32mm | 4mm | 1~6000mm (カスタム) |
45mm | 39mm | 3mm | 1~6000mm (カスタム) |
50mm | 44mm | 3mm | 1~6000mm (カスタム) |
50mm | 44mm | 3mm | 1~6000mm (カスタム) |
50mm | 44mm | 3mm | 1~6000mm (カスタム) |
50mm | 44mm | 3mm | 1~6000mm (カスタム) |
50mm | 44mm | 3mm | 1~6000mm (カスタム) |
50mm | 44mm | 3mm | 1~6000mm (カスタム) |
50mm | 44mm | 3mm | 1~6000mm (カスタム) |
50mm | 44mm | 3mm | 1~6000mm (カスタム) |
50mm | 44mm | 3mm | 1~6000mm (カスタム) |
50mm | 44mm | 3mm | 1~6000mm (カスタム) |
50mm | 42mm | 4mm | 1~6000mm (カスタム) |
50mm | 42mm | 4mm | 1~6000mm (カスタム) |
50mm | 42mm | 4mm | 1~6000mm (カスタム) |
50mm | 42mm | 4mm | 1~6000mm (カスタム) |
50mm | 42mm | 4mm | 1~6000mm (カスタム) |
50mm | 42mm | 4mm | 1~6000mm (カスタム) |
50mm | 40mm | 5mm | 1~6000mm (カスタム) |
50mm | 40mm | 5mm | 1~6000mm (カスタム) |
60mm | 54mm | 3mm | 1~6000mm (カスタム) |
60mm | 54mm | 3mm | 1~6000mm (カスタム) |
60mm | 54mm | 3mm | 1~6000mm (カスタム) |
60mm | 54mm | 3mm | 1~6000mm (カスタム) |
60mm | 52mm | 4mm | 1~6000mm (カスタム) |
60mm | 52mm | 4mm | 1~6000mm (カスタム) |
60mm | 50mm | 5mm | 1~6000mm (カスタム) |
60mm | 50mm | 5mm | 1~6000mm (カスタム) |
80mm | 74mm | 3mm | 1~6000mm (カスタム) |
80mm | 74mm | 3mm | 1~6000mm (カスタム) |
80mm | 74mm | 3mm | 1~6000mm (カスタム) |
80mm | 72mm | 4mm | 1~6000mm (カスタム) |
80mm | 72mm | 4mm | 1~6000mm (カスタム) |
80mm | 70mm | 5mm | 1~6000mm (カスタム) |
80mm | 70mm | 5mm | 1~6000mm (カスタム) |
85mm | 79mm | 3mm | 1~6000mm (カスタム) |
90mm | 80mm | 5mm | 1~6000mm (カスタム) |
100mm | 94mm | 3mm | 1~6000mm (カスタム) |
100mm | 94mm | 3mm | 1~6000mm (カスタム) |
100mm | 94mm | 3mm | 1~6000mm (カスタム) |
100mm | 92mm | 4mm | 1~6000mm (カスタム) |
100mm | 92mm | 4mm | 1~6000mm (カスタム) |
100mm | 90mm | 5mm | 1~6000mm (カスタム) |
100mm | 90mm | 5mm | 1~6000mm (カスタム) |
120mm | 112mm | 4mm | 1~6000mm (カスタム) |
120mm | 110mm | 5mm | 1~6000mm (カスタム) |
120mm | 112mm | 4mm | 1~6000mm (カスタム) |
120mm | 110mm | 5mm | 1~6000mm (カスタム) |
130mm | 120mm | 5mm | 1~6000mm (カスタム) |
130mm | 124mm | 3mm | 1~6000mm (カスタム) |
130mm | 124mm | 3mm | 1~6000mm (カスタム) |
130mm | 120mm | 5mm | 1~6000mm (カスタム) |
130mm | 120mm | 5mm | 1~6000mm (カスタム) |
140mm | 130mm | 5mm | 1~6000mm (カスタム) |
140mm | 130mm | 5mm | 1~6000mm (カスタム) |
150mm | 140mm | 5mm | 1~6000mm (カスタム) |
150mm | 140mm | 5mm | 1~6000mm (カスタム) |
150mm | 140mm | 5mm | 1~6000mm (カスタム) |
180mm | 170mm | 5mm | 1~6000mm (カスタム) |
180mm | 170mm | 5mm | 1~6000mm (カスタム) |
180mm | 170mm | 5mm | 1~6000mm (カスタム) |
200mm | 190mm | 5mm | 1~6000mm (カスタム) |
200mm | 190mm | 5mm | 1~6000mm (カスタム) |
200mm | 190mm | 5mm | 1~6000mm (カスタム) |
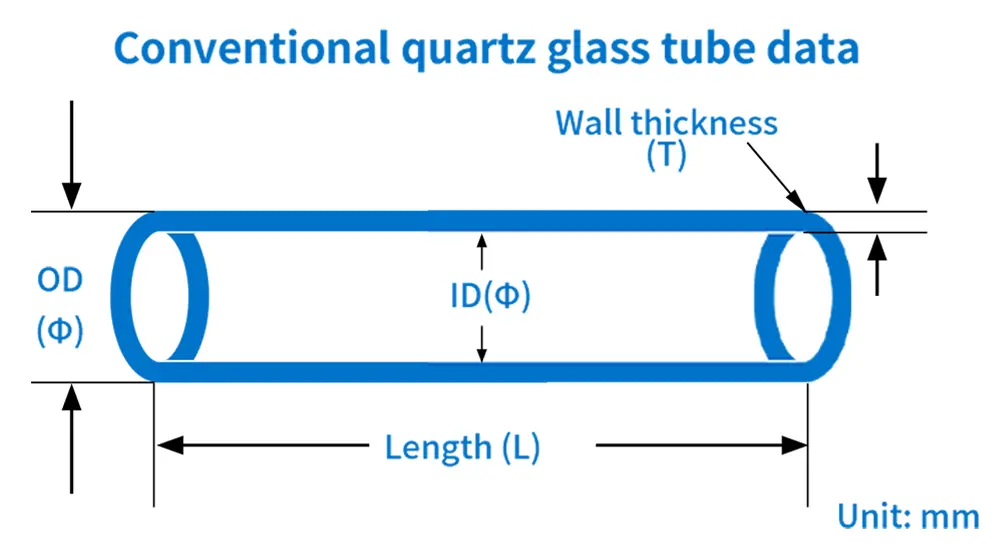
- 支払い方法:ご注文数量に応じて、銀行振込または前払い
- 納期:ご注文数量によります
- 輸送方法:お客様のご要望に応じて、海上輸送または航空輸送
備考:
注文を確定するために、以下のパラメータを提供いただく必要があります: ① 外径 (OD) ② 内径 (ID) ③ 肉厚 (WT) ④ 長さ (mm) ⑤ 数量
特性内容 | 特性値 |
---|---|
SiO2 | 99.99% |
密度 | 2.2×10³ kg/cm³ |
硬度 | モース硬度 5.5~6.5; ヌープ硬度 570 (荷重100g) |
引張強度 | 4.8 × 10⁷ Pa (48 N/mm² または 48 MPa); 7,000 psi |
圧縮強度 | >1.1×10⁹ Pa (160,000 psi) |
熱膨張係数 | 5.5×10⁻⁷ cm/cm·°C (20°C-320°C) |
熱伝導率 | 1.4 W/m-°C |
比熱 | 670 J/kg-°C |
軟化点 | 1730度C(3146度F) |
徐冷点 | 1210度C(2210度F) |
歪点 | 1120度C(2048度F) |
使用温度 | 1200°C |
電気抵抗率 | 7×10⁷Ωcm (350°C) |
サイズ | カスタマイズ対応 |
ロゴ | ロゴのカスタマイズ対応 |
高温耐性
石英ガラスは約1730℃のソフニングポイントを持ち、1100℃で連続使用できます。1450℃までの短期Exposureも可能です。これにより、曲げた石英ガラスチュービングは高温環境下で安定性を保ち、変形や損傷に耐えることができます。
優れた耐腐食性
フッ化水素酸を除いて、石英ガラスは他の酸に対してほとんど不活性です。酸に対する耐性はセラミックの30倍、ステンレス鋼の150倍です。したがって、曲げた石英ガラスチューブは、広範囲の腐食性媒体にさらされても耐えることができます。
高光沢透過率
石英ガラスは、紫外線から赤外線までの広いスペクトル範囲で優れた光透過特性を示し、可視光の透過率は93%を超えます。このため、曲げた石英ガラスチューブは光学的透明性が要求されるアプリケーションに最適です。
低熱膨張係数
石英ガラスは非常に低い熱膨張係数を持ち、急激な温度変化に耐えることができます。この特性により、曲げられた石英ガラスのチューブは、温度変動が大きい環境でも形状と性能を維持します。
衝撃と振動を避ける
曲げた石英ガラスチューブは高い硬度と強度を持っていますが、使用中に亀裂や損傷を防ぐために衝撃や振動を避けることが不可欠です。
温度を適切に制御してください。
高温環境で曲がった石英ガラスチューブを使用する際は、変形や損傷を避けるために最大動作温度を超えないように温度を注意深く制御する必要があります。
化学物質との接触を避けてください。
曲げた石英ガラスチューブと強酸やアルカリなどの腐食性化学物質との直接接触を最小限に抑え、腐食や損傷を防ぎます。
定期メンテナンスとケア
曲がった石英ガラスチューブを定期的に点検し、メンテナンスを行うことで、潜在的な問題を迅速に特定し対処します。これにより、適切な機能を確保し、チューブの寿命を延ばすことができます。
石英曲げ管は、高い熱安定性、光学的透明度、化学的耐性、及び電気絶縁性を備えています。非常に高い温度に耐えることができ、熱膨張が少なく、UVおよび可視光を含む幅広い光スペクトルに対して非常に透明です。また、化学的に不活性で、高純度を保持し、高温でも優れた電気絶縁性を提供します。
高純度の石英曲げパイプは、高温炉、化学反応、分光法、半導体製造、UV滅菌、産業用加熱、光学デバイスで使用されます。その多用途性は、半導体製造、研究室研究、UV滅菌、および光学フォトニクスなどの業界において不可欠です。
石英曲げ管は、高純度の石英砂を高温で溶融する特別なプロセスによって製造されます。このプロセスは、管が高い純度(99.99% SiO2)、高い透明度、およびその他の重要な特性を維持することを保証します。
よくある質問
当社は、高純度石英ガラス部品の一貫製造を専門としております。主な製品ラインナップは以下の通りです:
石英管・石英棒: 幅広い直径と仕様。
石英プレート・ディスク: 光学および工業用途向けに精密に切断・研磨。
石英実験器具: ビーカー、フラスコ、ボートなど、標準品から特注品まで幅広い種類のガラス器具。
半導体グレード石英: 半導体製造用のプロセスチューブやキャリアなどの高純度部品。
特注加工部品: お客様固有の設計および仕様に合わせて、複雑な部品を製造できます。
はい。特注加工(カスタム加工)は、当社の事業の中核です。10年以上にわたる専門的な経験を活かし、お客様企業と提携し、専門的なOEM/ODMサービスを提供しております。当社の加工技術には、溶接、研削、穴あけ、研磨、曲げ加工、その他さまざまな精密加工技術が含まれており、お客様の厳密なご要望にお応えする部品を製造いたします。
品質は当社の製造プロセスにおいて最も重要です。当社はISO 9001:2015認証取得メーカーであり、当社のプロセスが国際的な品質管理基準を満たしていることを保証します。また、当社の製品は純度と性能に関して厳格なSGS試験を受けています。当社は高純度原材料(SiO2 99.998%まで)を使用し、優れた熱安定性、高温耐性、化学的不活性を持つ溶融石英および溶融シリカ製品を製造しています。
当社はプロセスを最大限に効率化しました:
RFQ(見積依頼)を提出:ウェブサイトのお問い合わせフォームまたはEメールで、技術図面、仕様、要件をお送りください。
迅速な対応: 数分以内に初回返信を、30分以内に詳細なご連絡を差し上げます。
設計・提案:24時間以内に詳細な設計提案と競争力のある見積もりをお届けします。
試作・生産:承認後、お客様の納期に間に合わせるため、迅速に試作から本格的な量産へと移行いたします。
Aoxin Quartzとの提携には、いくつかの重要なメリットがあります:
実証された専門知識:業界で10年以上の経験を持つ当社には、複雑な課題に取り組むための技術的知見があります。
One-Stop Solution: We manage the entire production process, from sourcing high-purity raw materials to fabricating and finishing complex components.
競争力のある価値:主要な石英生産拠点に位置することで、効率的なサプライチェーンと先進的な製造技術を活用し、競争力のある価格で卓越した品質を提供しています。
Dedicated Partnership: Over 90% of our clients become long-term partners. We are committed to your success through responsive service, reliable quality, and innovative solutions.