Our advanced laser drilling capabilities allow for the creation of precise, micro-sized holes, complex patterns, and intricate features directly into high-purity quartz glass tubes and fused silica tubing. This non-contact process ensures exceptional accuracy, minimal material stress, and clean, burr-free edges, making it ideal for applications demanding the highest geometric precision. From microfluidic channels and analytical instrument nozzles to optical apertures and semiconductor components, our custom laser-drilled quartz tube solutions are engineered to meet your exact specifications for diameter, depth, and placement. Leverage the superior thermal, chemical, and optical properties of quartz with the unmatched precision of laser processing in tube form.
Property Content | Property Values |
---|---|
SiO2 | 99.99% |
Density | 2.2×10³ kg/cm³ |
Hardness | 5.5 - 6.5 Mohs' Scale 570 KHN 100 |
Tensile Strength | 4.8×10⁷ Pa (N/mm2) (7000 psi) |
Compression Strength | >1.1×10⁹ Pa (160,000 psi) |
Coefficient of Thermal Expansion | 5.5×10⁻⁷ cm/cm·°C (20°C-320°C) |
Thermal Conductivity | 1.4 W/m·°C |
Specific Heat | 670 J/kg·°C |
Softening Point | 1730°C (3146°F) |
Annealing Point | 1210°C (2210°F) |
Strain Point | 1120°C (2048°F) |
Work Temperature | 1200°C (2192°F) |
Electrical Resistivity | 7×10⁷ ohm cm (350°C) |
Size | Customized |
Logo | Customized Logo Accept |
Laser drilling utilizes a high-energy laser beam to ablate or melt quartz tube material, thereby creating holes. The high energy density and precise focusing of the laser beam enable a rapid and accurate drilling process, while also preventing material damage and deformation often associated with traditional mechanical drilling.”
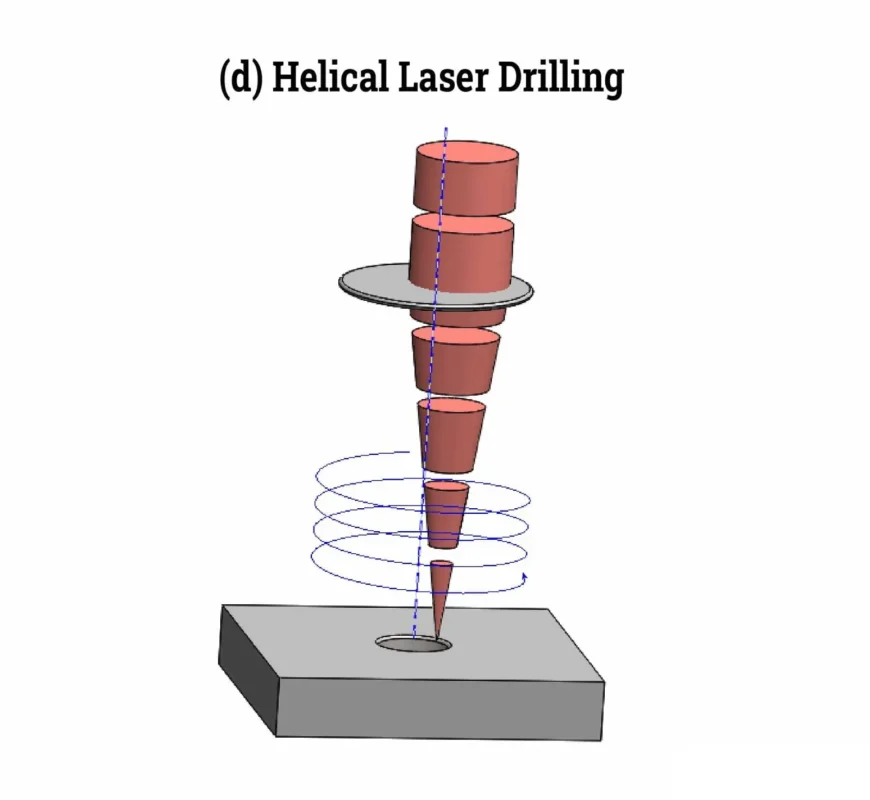
High Precision
Laser drilling enables high-precision hole creation, ensuring the accuracy of quartz tube machining and the quality of the final product. Achievable hole diameters can be as small as 1 micrometer, meeting the requirements of micro-fabrication.
High Efficiency
Laser drilling is a highly efficient machining method, capable of completing large-volume drilling tasks in a short time, thereby increasing production efficiency. The perforation speed is 10 to 1000 times faster than traditional mechanical equipment.
Non-Contact Process
Laser drilling is a non-contact machining method that avoids any damage or contamination to the surface of the quartz tube, ensuring the integrity of the final product.
Excellent Controllability
Laser drilling technology allows for the creation of holes of various shapes and sizes based on the actual requirements. Through adjusting laser power and processing parameters, precise control over hole size and shape can be achieved.
Equipment Selection
When choosing laser drilling equipment, select appropriate models and configurations based on processing needs and budget. Furthermore, consider the brand and quality of the equipment to ensure its stability and reliability.
Process Parameter Adjustment
During processing, adjust parameters based on the material, thickness, and processing requirements of the quartz tube to achieve optimal results.
Safety Precautions
Laser drilling generates intense laser radiation and high temperatures. Therefore, safety precautions such as wearing protective eyewear and clothing must be followed.
Maintenance and Upkeep
Regularly maintain the laser drilling equipment, including cleaning the lens, checking the cooling system, and replacing worn parts, to ensure normal operation and extend the equipment’s lifespan.”
Frequently asked questions
We specialize in the end-to-end manufacturing of high-purity quartz glass components. Our core product lines include:
Quartz Tubing & Rods: A wide range of diameters and specifications.
Quartz Plates & Discs: Precision-cut and polished for optical and industrial use.
Quartz Labware: A full suite of standard and custom glassware, including beakers, flasks, and boats.
Semiconductor-Grade Quartz: High-purity components like process tubes and carriers for semiconductor fabrication.
Custom Fabricated Components: We can produce complex parts tailored to your unique designs and specifications.
Yes. Custom fabrication is at the core of our business. With over a decade of specialized experience, we partner with companies to provide expert OEM/ODM services. Our capabilities include welding, grinding, drilling, polishing, bending, and other precision processing techniques to create components that meet your exact requirements.
Quality is paramount in our manufacturing process. We are an ISO 9001:2015 certified manufacturer, ensuring that our processes meet international quality management standards.Our products also undergo rigorous SGS testing for purity and performance. We use high-purity raw materials (up to 99.998% SiO2) to produce fused quartz and fused silica products with exceptional thermal stability, high-temperature resistance, and chemical inertness.
We've streamlined our process to be as efficient as possible:
Submit Your RFQ: Send us your technical drawings, specifications, and requirements via our website contact form or email.
Rapid Response: You can expect an initial response within minutes and detailed communication within half an hour.
Design & Proposal: We will deliver a detailed design proposal and a competitive quote within 24 hours.
Prototyping & Production: Upon approval, we move swiftly from prototyping to full-scale production to meet your deadlines.
Partnering with Aoxin Quartz offers several key advantages:
Proven Expertise: With 10+ years in the industry, we have the technical knowledge to tackle complex challenges.
One-Stop Solution: We manage the entire production process, from sourcing high-purity raw materials to fabricating and finishing complex components.
Competitive Value: Located in a major quartz production hub, we leverage an efficient supply chain and advanced manufacturing to offer exceptional quality at a competitive price point.
Dedicated Partnership: Over 90% of our clients become long-term partners. We are committed to your success through responsive service, reliable quality, and innovative solutions.