Quartz laser-drilled glass plates refer to products in which holes are created on quartz glass plates using laser drilling technology. Quartz glass, due to its excellent properties such as high light transmission, high hardness, high-temperature resistance, and corrosion resistance, is widely used in many fields. Laser drilling technology, with its high precision, high efficiency, and non-contact nature, has become an important method for processing quartz glass plates.
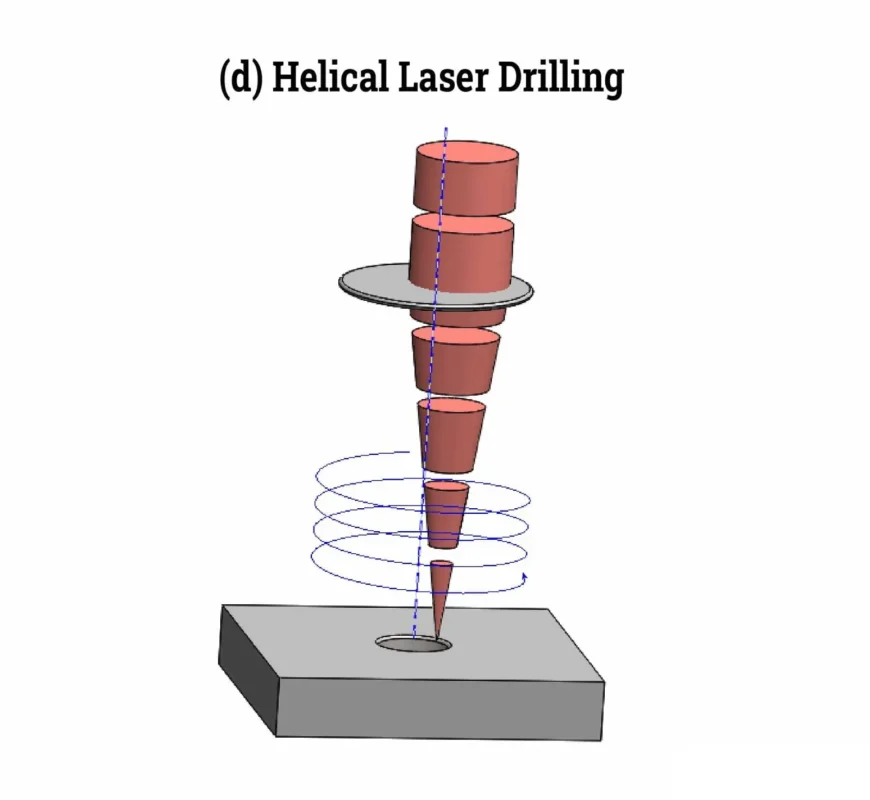
The principle behind laser drilling of quartz glass plates mainly involves using a high-energy density laser beam to focus and locally heat the quartz glass. This causes the quartz glass to undergo thermal expansion, thereby creating holes at the designated locations. The high energy and precise focusing of the laser beam result in a highly accurate and rapid processing, while also avoiding material damage and stress concentrations that can occur with traditional mechanical drilling methods.
Property Content | Property Values |
---|---|
SiO2 | 99.99% |
Density | 2.2×10³ kg/cm³ |
Hardness | 5.5 - 6.5 Mohs' Scale 570 KHN 100 |
Tensile Strength | 4.8×10⁷ Pa (N/mm2) (7000 psi) |
Compression Strength | >1.1×10⁹ Pa (160,000 psi) |
Coefficient of Thermal Expansion | 5.5×10⁻⁷ cm/cm·°C (20°C-320°C) |
Thermal Conductivity | 1.4 W/m·°C |
Specific Heat | 670 J/kg·°C |
Softening Point | 1730°C (3146°F) |
Annealing Point | 1210°C (2210°F) |
Strain Point | 1120°C (2048°F) |
Work Temperature | 1200°C (2192°F) |
Electrical Resistivity | 7×10⁷ ohm cm (350°C) |
Size | Customized |
Logo | Customized Logo Accept |
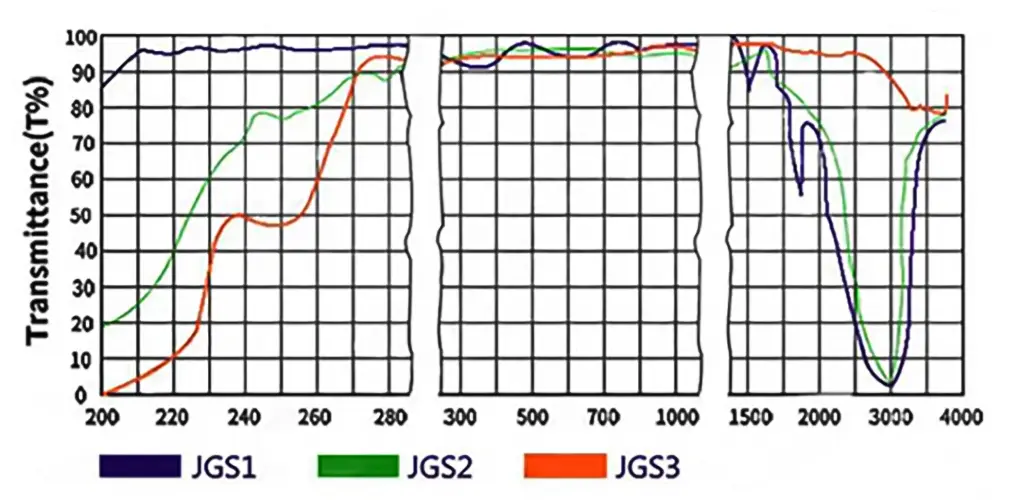
JGS1
Commonly known as UV-grade fused silica, this material exhibits exceptionally low dispersion and very high transmittance in the ultraviolet (UV) spectral range.
JGS2
Similar to JGS1, but may have variations in specific performance parameters such as transmittance and thermal expansion coefficient, depending on the manufacturer’s standards.
JGS3
Typically used in applications requiring higher purity or specialized performance characteristics. Specific performance parameters can vary based on the manufacturer.
High Precision
Laser drilling technology can achieve processing precision at the micrometer and even nanometer level, meeting the requirements of high-precision applications.
High Efficiency
Laser drilling speeds are much faster than traditional mechanical drilling methods, significantly improving production efficiency.
Non-Contact Processing
During laser drilling, the laser beam does not make direct contact with the material, avoiding material damage caused by mechanical stress.
High Flexibility
Laser drilling can be performed on irregular surfaces, and hole patterns or complex shapes can be set up arbitrarily.
Application Scenario
Frequently asked questions
We specialize in the end-to-end manufacturing of high-purity quartz glass components. Our core product lines include:
Quartz Tubing & Rods: A wide range of diameters and specifications.
Quartz Plates & Discs: Precision-cut and polished for optical and industrial use.
Quartz Labware: A full suite of standard and custom glassware, including beakers, flasks, and boats.
Semiconductor-Grade Quartz: High-purity components like process tubes and carriers for semiconductor fabrication.
Custom Fabricated Components: We can produce complex parts tailored to your unique designs and specifications.
Yes. Custom fabrication is at the core of our business. With over a decade of specialized experience, we partner with companies to provide expert OEM/ODM services. Our capabilities include welding, grinding, drilling, polishing, bending, and other precision processing techniques to create components that meet your exact requirements.
Quality is paramount in our manufacturing process. We are an ISO 9001:2015 certified manufacturer, ensuring that our processes meet international quality management standards.Our products also undergo rigorous SGS testing for purity and performance. We use high-purity raw materials (up to 99.998% SiO2) to produce fused quartz and fused silica products with exceptional thermal stability, high-temperature resistance, and chemical inertness.
We've streamlined our process to be as efficient as possible:
Submit Your RFQ: Send us your technical drawings, specifications, and requirements via our website contact form or email.
Rapid Response: You can expect an initial response within minutes and detailed communication within half an hour.
Design & Proposal: We will deliver a detailed design proposal and a competitive quote within 24 hours.
Prototyping & Production: Upon approval, we move swiftly from prototyping to full-scale production to meet your deadlines.
Partnering with Aoxin Quartz offers several key advantages:
Proven Expertise: With 10+ years in the industry, we have the technical knowledge to tackle complex challenges.
One-Stop Solution: We manage the entire production process, from sourcing high-purity raw materials to fabricating and finishing complex components.
Competitive Value: Located in a major quartz production hub, we leverage an efficient supply chain and advanced manufacturing to offer exceptional quality at a competitive price point.
Dedicated Partnership: Over 90% of our clients become long-term partners. We are committed to your success through responsive service, reliable quality, and innovative solutions.