Quartz press bars are a critical component widely used in the manufacturing and repair of electronic devices, particularly in hot press equipment and within the LCD industry.
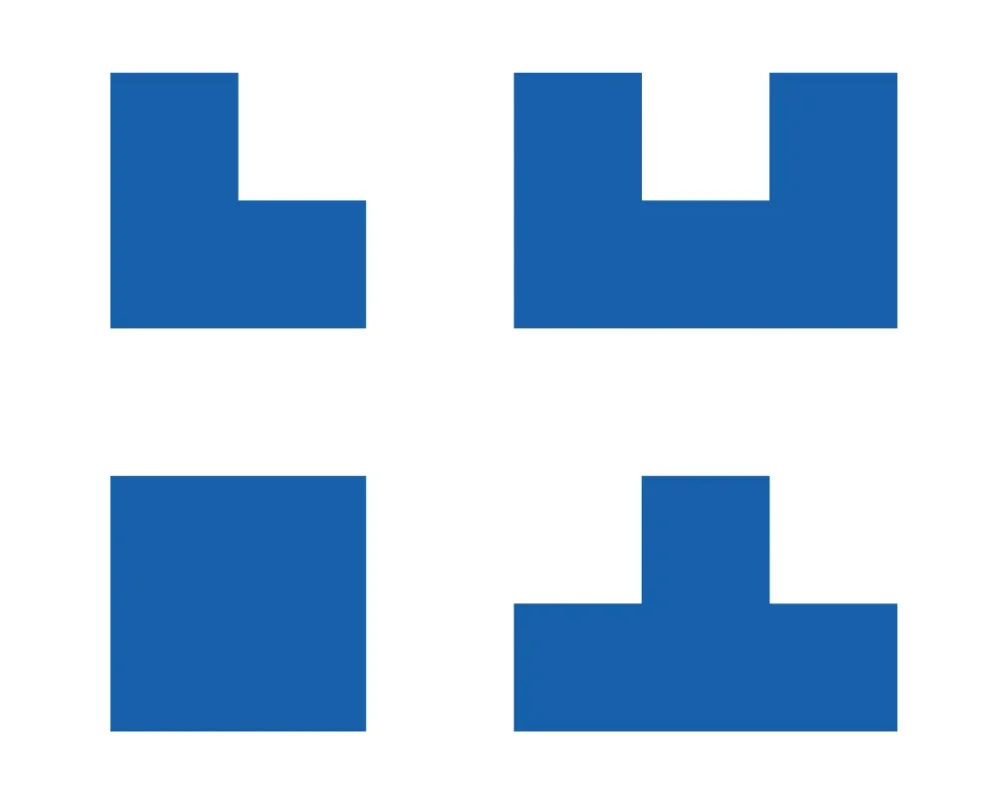
Quartz press bars can be custom-manufactured to meet specific customer requirements, including various shapes (such as L-shaped, T-shaped, square bars, double-stepped, etc.), dimensions, and precision levels. Professional manufacturers possess advanced processing equipment and extensive manufacturing experience, enabling them to provide customers with high-quality, high-precision quartz press bar products.
Property Content | Property Values |
---|---|
SiO2 | 99.99% |
Density | 2.2×10³ kg/cm³ |
Hardness | 5.5 - 6.5 Mohs' Scale 570 KHN 100 |
Tensile Strength | 4.8×10⁷ Pa (N/mm2) (7000 psi) |
Compression Strength | >1.1×10⁹ Pa (160,000 psi) |
Coefficient of Thermal Expansion | 5.5×10⁻⁷ cm/cm·°C (20°C-320°C) |
Thermal Conductivity | 1.4 W/m·°C |
Specific Heat | 670 J/kg·°C |
Softening Point | 1730°C (3146°F) |
Annealing Point | 1210°C (2210°F) |
Strain Point | 1120°C (2048°F) |
Work Temperature | 1200°C (2192°F) |
Electrical Resistivity | 7×10⁷ ohm cm (350°C) |
Size | Customized |
Logo | Customized Logo Accept |
High Light Transmittance
Quartz press bars exhibit extremely high light transmittance, typically reaching 99% or greater, ensuring efficient light transmission during pressing processes.
Excellent Flatness
Their surface flatness is exceptionally high, often achieving ±0.002mm, which facilitates high-precision pressing operations.
High-Temperature and Chemical Resistance
The quartz material demonstrates outstanding resistance to high temperatures and chemical substances, maintaining stability even in harsh working environments.
High Hardness
Quartz has a high hardness, providing the press bars with good wear resistance and scratch resistance during use.
Application Scenario
Handle with Care
Quartz glass products are valuable materials and must be handled with care to avoid collisions and drops.
Temperature Limits
All types of quartz glass have a maximum operating temperature. This temperature should not be exceeded, as it may result in devitrification or softening and deformation.
Cleaning Procedures
Quartz glass products intended for high-temperature use must be thoroughly cleaned before use. This can be accomplished by soaking in a suitable cleaning solution, followed by rinsing with high-purity water or treatment with alcohol.
Avoid Thermal Shock
Although quartz glass has good thermal stability, variations in residual stress and product shape can result in varying levels of thermal shock resistance. These differences should be taken into consideration during use.
Prevent Contact with Alkaline Substances
As an acidic material, quartz glass should be kept away from alkaline substances (such as water glass, asbestos, and compounds of potassium and sodium), particularly at high temperatures, as contact will significantly reduce its crystallization resistance.
Frequently asked questions
We specialize in the end-to-end manufacturing of high-purity quartz glass components. Our core product lines include:
Quartz Tubing & Rods: A wide range of diameters and specifications.
Quartz Plates & Discs: Precision-cut and polished for optical and industrial use.
Quartz Labware: A full suite of standard and custom glassware, including beakers, flasks, and boats.
Semiconductor-Grade Quartz: High-purity components like process tubes and carriers for semiconductor fabrication.
Custom Fabricated Components: We can produce complex parts tailored to your unique designs and specifications.
Yes. Custom fabrication is at the core of our business. With over a decade of specialized experience, we partner with companies to provide expert OEM/ODM services. Our capabilities include welding, grinding, drilling, polishing, bending, and other precision processing techniques to create components that meet your exact requirements.
Quality is paramount in our manufacturing process. We are an ISO 9001:2015 certified manufacturer, ensuring that our processes meet international quality management standards.Our products also undergo rigorous SGS testing for purity and performance. We use high-purity raw materials (up to 99.998% SiO2) to produce fused quartz and fused silica products with exceptional thermal stability, high-temperature resistance, and chemical inertness.
We've streamlined our process to be as efficient as possible:
Submit Your RFQ: Send us your technical drawings, specifications, and requirements via our website contact form or email.
Rapid Response: You can expect an initial response within minutes and detailed communication within half an hour.
Design & Proposal: We will deliver a detailed design proposal and a competitive quote within 24 hours.
Prototyping & Production: Upon approval, we move swiftly from prototyping to full-scale production to meet your deadlines.
Partnering with Aoxin Quartz offers several key advantages:
Proven Expertise: With 10+ years in the industry, we have the technical knowledge to tackle complex challenges.
One-Stop Solution: We manage the entire production process, from sourcing high-purity raw materials to fabricating and finishing complex components.
Competitive Value: Located in a major quartz production hub, we leverage an efficient supply chain and advanced manufacturing to offer exceptional quality at a competitive price point.
Dedicated Partnership: Over 90% of our clients become long-term partners. We are committed to your success through responsive service, reliable quality, and innovative solutions.